Air Curtains For Comfortable Environments
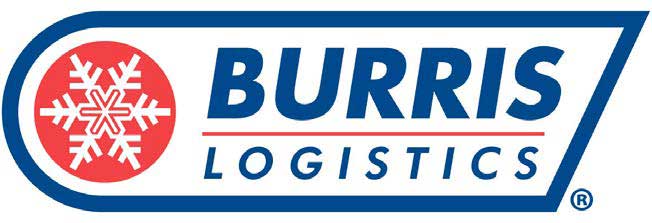
Challenge
Cold storage warehousing and facility management requires specialized skills in perishable product control, and can be costly if poorly managed.The mission-critical role for facility operators is to control everything from cold storage freeze times to equipment safety – all while condensation, slippery floors, icing, freezing doors, frosting, and fogging endanger product quality, threaten staff safety, and all but guarantee high utility spend. And with industry growth predicted to run 3.4% in 2019, the mandate for best in class processes for optimal cold storage performance will only rise.
When international third-party logistics leader Burris Logistics, specializing in customized retail distribution services, encountered fogging and frosting on their bi-parting high speed doors in their Lakeland, Florida facility, they sought out a solution to provide unequivocal resolution of the issues without significant management oversight or cost. With a 118,561 sq. ft facility hosting over 108,000 sq. ft (3,343,990 cubic feet) of refrigerated space, the need for their refrigerated system to operate at peak performance is a must to maintain product integrity, keep the staff comfortable, eliminate injuries tied to condensation and slippery floors, and reduce the utility spend.
The Solution
With the Florida climate, (known for high temperatures and higher humidity), driving many of the issues that hindered operations at the Lakeland plant, the Mars engineering team joined with facility operators to identify a set of 8 ft x 14 ft doors that were responsible for one hundred 17-second cycles per hour for an average of 9 hours each day. The effort to resolve the plant's issues began with Mars specialized cold storage survey that guides the Mars team to select the specialized components in Mars Freezer package – the secret sauce that allows Mars to resolve the thorniest of cold storage issues. The assessment led to the selection of Mars High Velocity heated units (HV2108-2EON-TS-FP) )which were set atop an adjustable mounting bracket paired with an industrial magnetic switch. The electric heated air curtain with freezer package included:
- Humidistat to deploy heat to combat condensation issues during periods of high ambient humidity
- Mars' custom heat-on-demand sequence, to dry condensation buildup after doors close (capable of being stopped when not needed)
- Time delay functionality, to dry any condensation upon door closure
- 2-speed switch for the motor
Facility operators quickly saw results. The Mars units effectively eliminated the fog, condensation, and snow-like effects on the Rytech high-speed door.
STUDIES REVEAL A 6%-9% UPSIDE EFFECT ON WORK PERFORMANCE BASED ON IMPROVED AIR QUALITY AND TEMPERATURE. (WYON 2004)
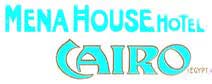
PRODUCING NON-TRADITIONAL SOLUTIONS
To make sure frozen food keeps its sensory and nutritional quality, as well as maintain food safety standards, temperature requirements have been set for every stage of the cold storage chain.No less a consideration is the hit to food storage life when products are exposed to temperature fluctuations. In challenging environments, the mere act of moving food from a transport truck to a freezer can raise the temperature of the food significantly and tax a cooling system as it struggles to return to the thermostat set point. The Mena House Hotel in heat-steeped Cairo, Egypt has welcomed dignitaries such as Winston Churchill, Queen Mary, and Richard Nixon... as well as average summer temperatures of 94°F to 104°F. With a bank of 20 foot by 20 foot freezers that needed frequent stocking to keep hotel guests fed, a significant solution was needed to unburden the freezer compressors, protect the food from heating up, and give some relief from rising energy costs. Using a series of 42-inch custom-engineered models, the Mars Air Systems engineering team was able to create a wall of cold air to halt the incursion of heat and dust. The air curtains eliminated temperature fluctuations, reduced the stress on the equipment, and helped reduce burgeoning energy costs.
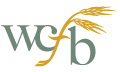
TOO MANY PEOPLE NEED US – IT HAS TO BE RIGHT
When you’re as successful as Westmoreland County Food Bank, you serve 7,200 families a month and operate a 40,000 sq.ft. facility that processes 8.6 million pounds of food a year - and your food storage equipment needs to work flawlessly.For Westmoreland, facility limitations forced the freezer and evaporator to sit side-by-side, which caused excessive humidity that led to ice and frost on the floor outside the freezer doorway – a safety hazard for both forklifts and workers on foot. When it’s too important or costly to be anything other than right, Mars Air Systems is the team you want on your side. Mars has been repeatedly the source for answers when large industrial and foodservice operators need no-fail solutions to vexing humidity, unwanted condensation, or hazardous pools of water. Deploying air baffles along side the series of air curtains gave the Westmoreland workers the means to ward off the flowing water that had been a source of slippage, falls, and worker injury.
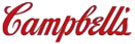
PUTTING THE SKIDS ON SLIPPERY
Campbell Soup Company, one of the largest food companies in the world, operates a sprawling, 2.4 million-sq.-ft. facility on a 949-acre parcel, which includes operating a cooler/freezer storage unit 24 hours/day alongside a 8’x16’ heavily trafficked forklift entrance with a fast-acting vertical-lift door.The hot, humid warehouse conditions collide with the cold, dry-storage area air which produces condensation and pools of water at the base of the freezer -- both inside and out. Pooled water also flows from the freezer opening directly into the walkways, interfering with both foot and forklift traffic. The Mars engineering team identified the precise area that needed an air stream to eliminate condensation, then installed a stack of vertically-mounted, door-activated air curtains and air diffusers* at the cold storage unit’s forklift entrance. The air curtain’s forced-air action stabilized cold area temperatures by creating an air seal which effectively evaporated most of the surface condensation, while also eliminating pools of water in the walkway.
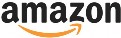
THE KING OF SHIPPING FINDS A DEPENDABLE PARTNER
When you process and ship of more than 1 billion packages a year through more than 150 fulfillment and sorting centers, those vast working spaces need to be consistently clean and comfortable despite dozens of wide openings for people and equipment to pass through 24/7. One Amazon center is so large it’s the size of 28 football fields. These facilities are known to have internal temps reach over 90°F, which is a common challenge for large industrial spaces. And, while goods move in and out as quickly, employees are long-term guests who have to deal with the air quality and temperature constraints for hours each day, year after year. Industrial facility managers need consistent durable solutions customized for their unique climate and constraints. So Amazon’s facility managers called in the titan of tough. Across the U.S., the Mars air curtain now stands guard at Amazon fulfillment and sorting facilities and manages their many large dock doors. They safeguard against air transfer and pollutant infiltration, while keeping passages free and clear from obstructions that lead to accidents.